The Swedish Energy Agency supports Stena Recycling in battery recycling
The Swedish Energy Agency gives Stena Recycling SEK 70.7 million in support for the investment in a new battery recycling plant in Halmstad. Stena Recycling's target is to become one of Europe's leading players in the recycling of lithium-ion batteries.
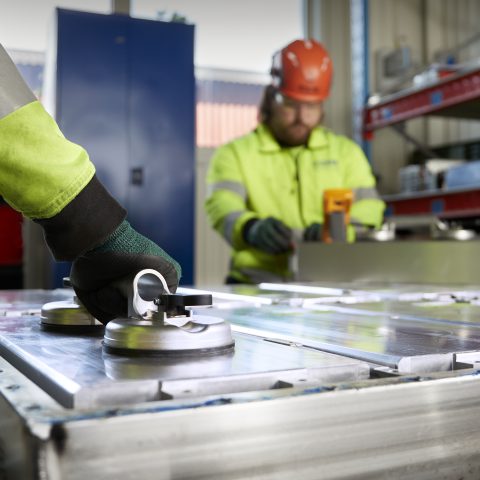
The Swedish Energy Agency gives Stena Recycling SEK 70.7 million in support for the investment in a new battery recycling plant in Halmstad. Stena Recycling’s target is to become one of Europe’s leading players in the recycling of lithium-ion batteries, a theme that we have recently addressed here too.
Stena Recycling is now intensifying its work on the construction of the new recycling plant in Halmstad. The facility is expected to initially handle around 10,000 tonnes of batteries per year. This will include lithium-ion batteries from electric cars as well as industrial and consumer products. In addition, battery centers are being established around Europe to ensure an infrastructure for collecting the batteries.
“We are very pleased that the Swedish Energy Agency has granted our application and see it as important and natural to contribute to closing the loop of valuable materials contained in batteries. We are introducing an advanced technology and it is exciting that we are now breaking new ground and setting the standard in battery recycling. Our goal is to have the plant operational in the first quarter of 2023,” says Fredrik Pettersson, CEO of Stena Recycling Sweden.
Stena Recycling’s investment in battery recycling aims to meet the substantial increase of batteries predicted in society, and to stay ahead of the EU directive that is scheduled to come into force from 2025. The directive will impose stricter requirements on battery recycling and the recovery of valuable materials such as cobalt, lithium and nickel, which in turn will reduce the need for the extraction of virgin minerals and metals.
Stena Recycling: advanced battery recycling technology
There are currently only a few recycling facilities for lithium-ion batteries from hybrid and electric cars in Europe. These use melting furnaces in the final stages of the recycling process, which produce high carbon dioxide emissions.
Stena Recycling has chosen a new technology for the recycling of lithium-ion batteries that is expected to provide a higher recycling rate and a lower climate impact than existing melting furnace technology. In short, the technology is based on grinding batteries in an inert environment. This is followed by an advanced process to separate the different fractions in order to recover valuable metals. From the black mass, which is one of the fractions from batteries, nickel, cobalt, and lithium, among others, are extracted in the next step.
By establishing Sweden’s first lithium-ion battery recycling plant, the battery waste will not have to be sent for export but can be handled domestically. This is positive from both a social and environmental perspective, as well as important for Swedish industry, which will have access to recycled raw materials at home.